Industrial equipment must be upgraded from time to time for a company to remain competitive. Delaying modernization allows competitors to reap the benefits of new technology, like increased efficiency, decreased production costs, and higher quality end products. If this situation persists for too long, a company can lose their advantages that have historically made them successful and be left in the dust. But upgrading industrial equipment is a very expensive proposition — the equipment itself is very costly, and the time that the present equipment is taken out of service to perform the upgrade will impact production. Traditionally this has led to a precarious balancing act in which the heavy, immediate costs of upgrades have to be weighed against the future costs of aging and obsolete equipment.
In some cases, there may be a better upgrade path available that is both inexpensive and transparent to current operational processes. Edge machine learning specialist Simone Salerno recently demonstrated a method to upgrade the ubiquitous pallet-wrapping machines found in warehouses and manufacturing facilities around the globe. With the help of Edge Impulse and a low-cost microcontroller, he has shown how these simple machines can be extended to also act as weight scales. And as if that were not enough, he also gave the machines predictive maintenance capabilities using the same device. The upgrade can be added to an existing pallet-wrapping machine without the need for any downtime.
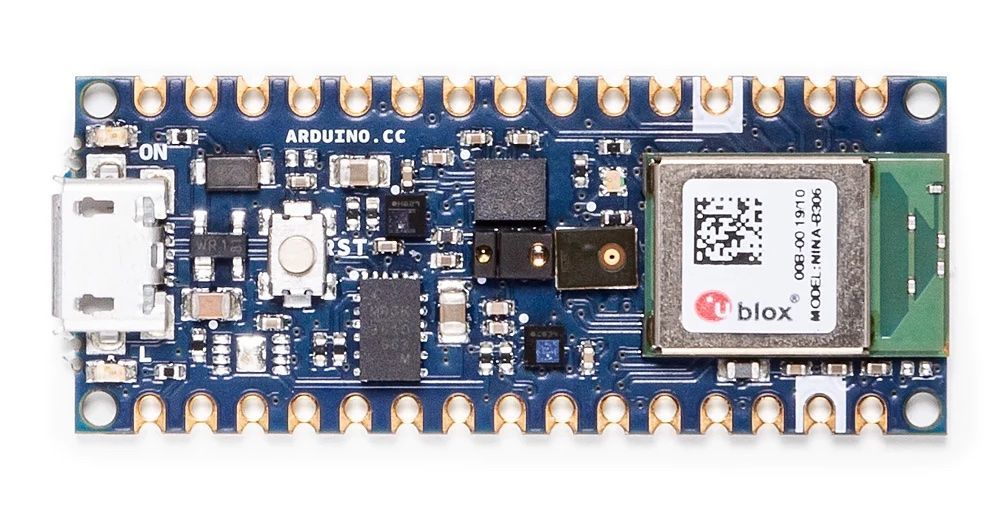
The basis for this project rests on the fact that a pallet-wrapping machine’s motor is subjected to friction as it spins, and that friction is proportionate to the weight on the platform. To put it into more plain terms, for a fixed rotation force, the platform will rotate slower when loaded with heavier weights. With that knowledge, it is possible to capture measurements from an accelerometer and gyroscope while the motor spins, and use a machine learning model to translate those measurements into a metric representing the weight loaded onto the machine. Once such a model has been built, it can also be used in another way — by loading a known weight on the machine and measuring it with the device, the difference between the weights (known and predicted) can be used to determine if there may be a problem with the pallet-wrapper. A large difference between the values suggests that maintenance may be in order.
Since Edge Impulse models can be deployed to many different hardware platforms, Salerno notes that the exact platform used is not terribly important. But in this case, he chose to use an Arduino Nano 33 BLE Sense because it has plenty of computing horsepower to run a highly-optimized machine learning model created with Edge Impulse, and it also comes standard with an onboard accelerometer. Additionally, there is a Bluetooth Low Energy radio, which enables the board to wirelessly communicate while on a spinning pallet-wrapper without worrying about cords getting twisted up.
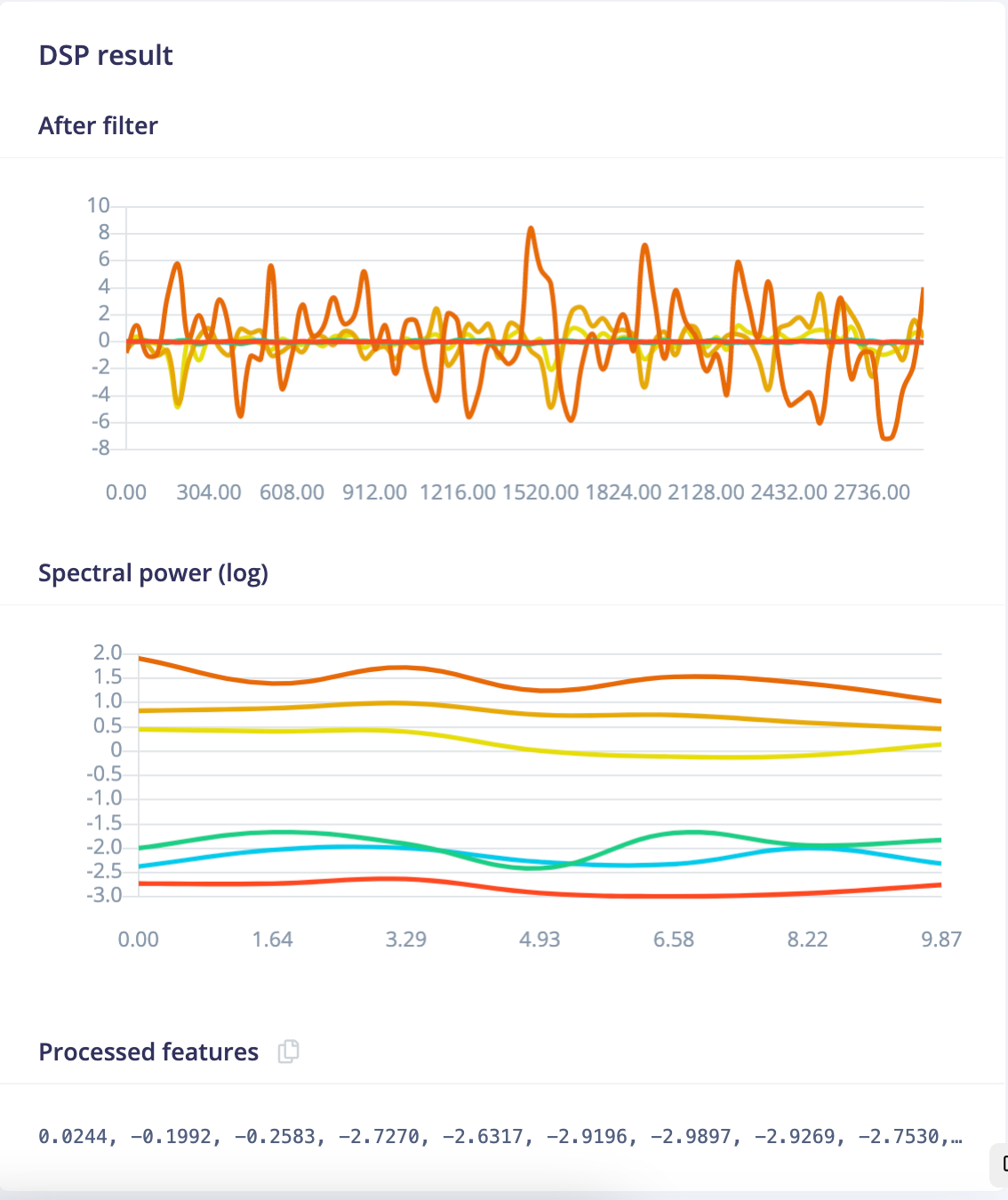
To give the model some intelligence, it needs example data to learn from. Salerno developed an Arduino sketch that streams accelerometer data over Bluetooth to a laptop that writes the measurements to a file. Using this setup, he streamed data with the pallet-wrapper loaded with a dozen different weights. A total of 30 seconds of sample data was collected for each weight level. WIth the training data saved as CSV-formatted files, they were ready to be uploaded to Edge Impulse using the data acquisition tool.
After uploading the training data, Salerno pivoted to the design of the impulse. A relatively large window of three seconds was chosen for splitting the data up to be sure that there was enough information for the model to learn from. A spectral analysis was conducted on the data from each window to highlight the most relevant features in the motion data, and to reduce the computational resources that would be needed later in the analysis pipeline. Finally, regression was chosen for the learning block because the project requires that continuous weight values be predicted. It was recommended that an iterative approach be used to choose the best model design — start with a small, two-layer network and see how it performs. If greater accuracy is needed, increase the size of the network. Starting small ensures that you will have the best performance possible after deploying the model to the physical hardware.
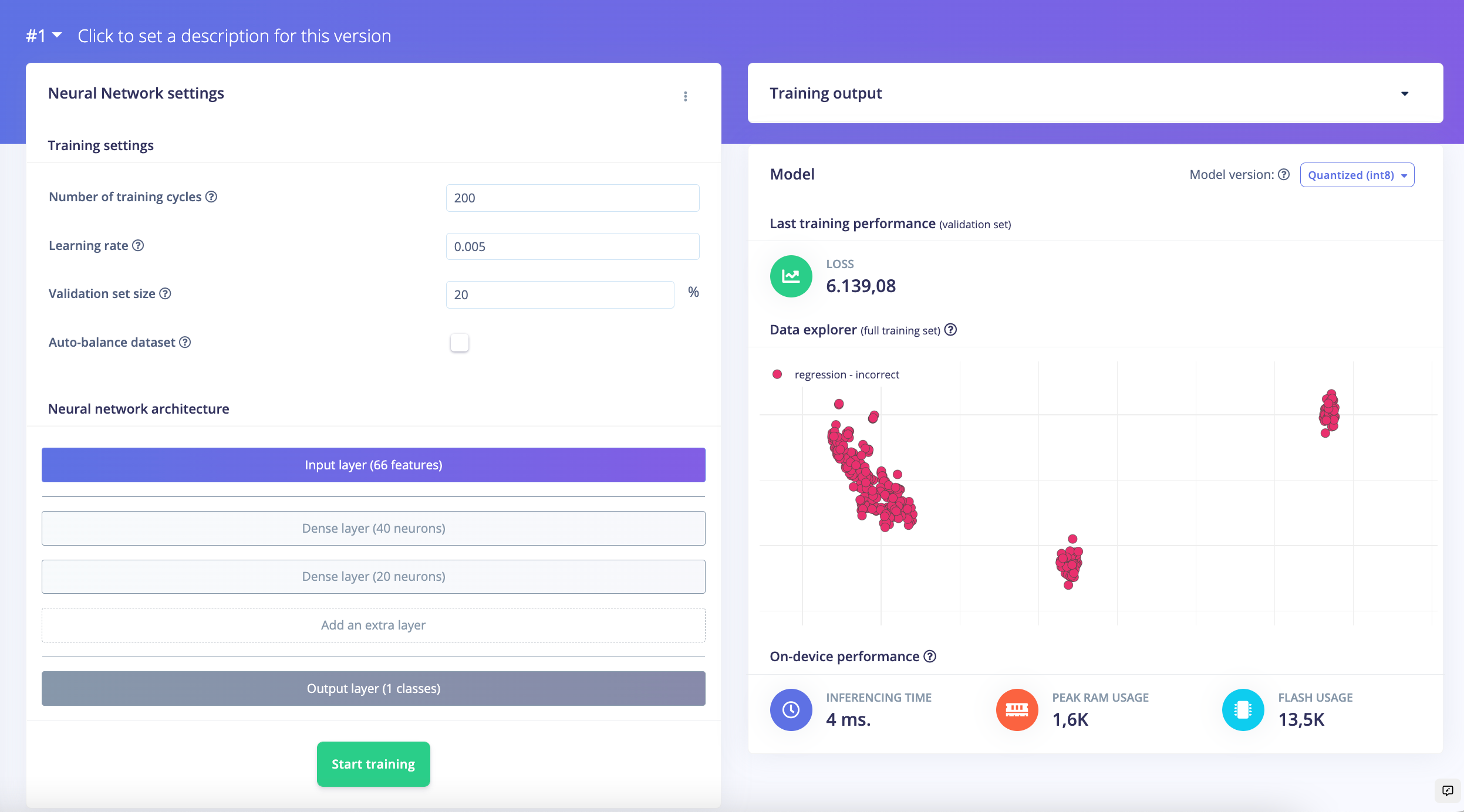
In this case, two layers was sufficient for good predictive power. With everything tuned and performing as expected, the machine learning pipeline was deployed to the Nano 33 BLE Sense. By deploying the model as an Arduino library, it was quick to get inferences running on the hardware, and it also offered the flexibility of including custom logic that is triggered based on those inference results.
To give a taste of what a final version of this weight sensor might look like, Salerno hooked a seven-segment display up to a second Nano 33 BLE Sense. This one sits next to the pallet-wrapper and shows the weight predictions made by the Arduino that is attached to the machine running the Edge Impulse algorithm.
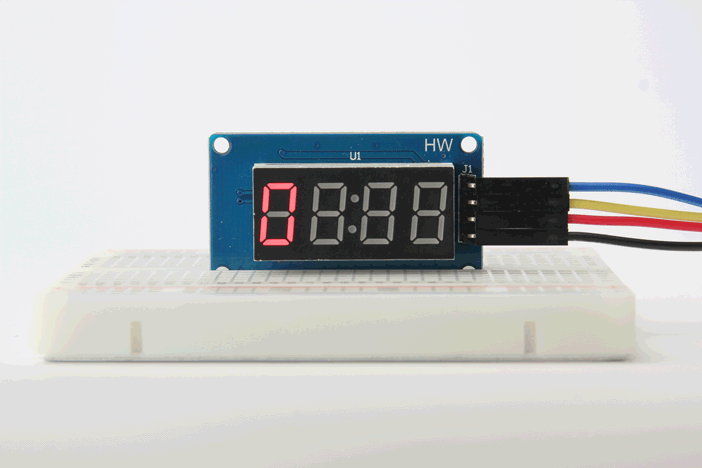
That’s a wrap! Upgrading industrial machinery by adding an intelligent algorithm can save a lot of money when compared with buying a new machine, and it also allows the present machines to keep operating during the upgrade process. That could be a huge win for many companies. And it is a lot easier than you might think to get started. Don’t believe me? Take a look at the project documentation to see how simple machine learning can be.
Want to see Edge Impulse in action? Schedule a demo today.