Anyone that has a 3D printer knows how useful it can be to be able to quickly and inexpensively print any arbitrary object on the spot. This technology has proven itself able to eliminate the long delays associated with sending a job to an outside manufacturer, and also allows unique items to be produced in single quantities. Clearly, 3D printers are good for a lot more than printing your favorite Pokémon character, and many industries have taken note. One area in particular that is being transformed by this technology is dentistry.
Dental casts are traditionally either cast in plaster or are milled. As compared with 3D-printed dental casts, these traditional options are lacking in sturdiness and detail, which leaves them poorly suited for certain uses, like identifying dental problems. After a quick intraoral scanning, the results can be handed off to a dental technician for in-office printing of the cast, then in short order the casts can be assessed by a dentist to assist in diagnosing problems. But despite the successes of 3D printers, these devices are not perfect and do go astray at times. Knowing that inaccurate prints may be produced without any warning is enough to make some dental practices think twice about using the technology at all.
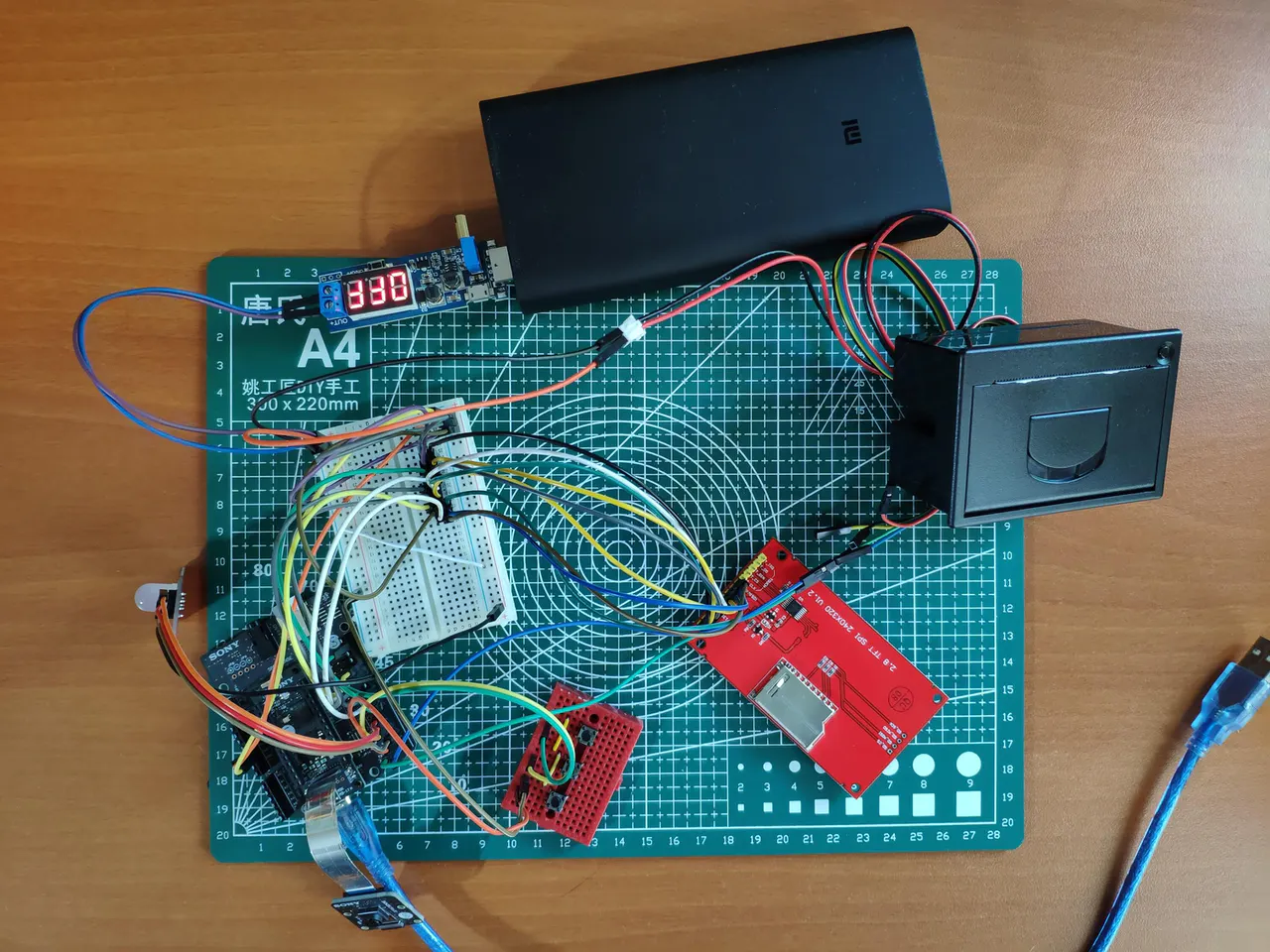
Engineer Kutluhan Aktar has taken notice of this problem and decided to design a solution that may restore the confidence of dentists in 3D-printed dental casts. He set out to build a computer vision system that can analyze casts to determine if they have been printed with a high degree of accuracy, or if something went wrong along the way. To separate the wheat from the chaff, Aktar built a machine learning object detection pipeline with the help of Edge Impulse.
For the hardware, a high-performance Sony Spresense development board was selected. The six-core Arm Cortex-M4F processor running at 156 MHz, and the 1.5 MB of SRAM make this platform ideal for running inferences on a highly-optimized model generated by Edge Impulse. A Sony Spresense camera was also added in to allow the device to capture images of dental casts to be inspected. To make the system accessible to dental technicians, Aktar designed a 3D-printed case, and added an LCD touchscreen display and thermal printer to present the results.
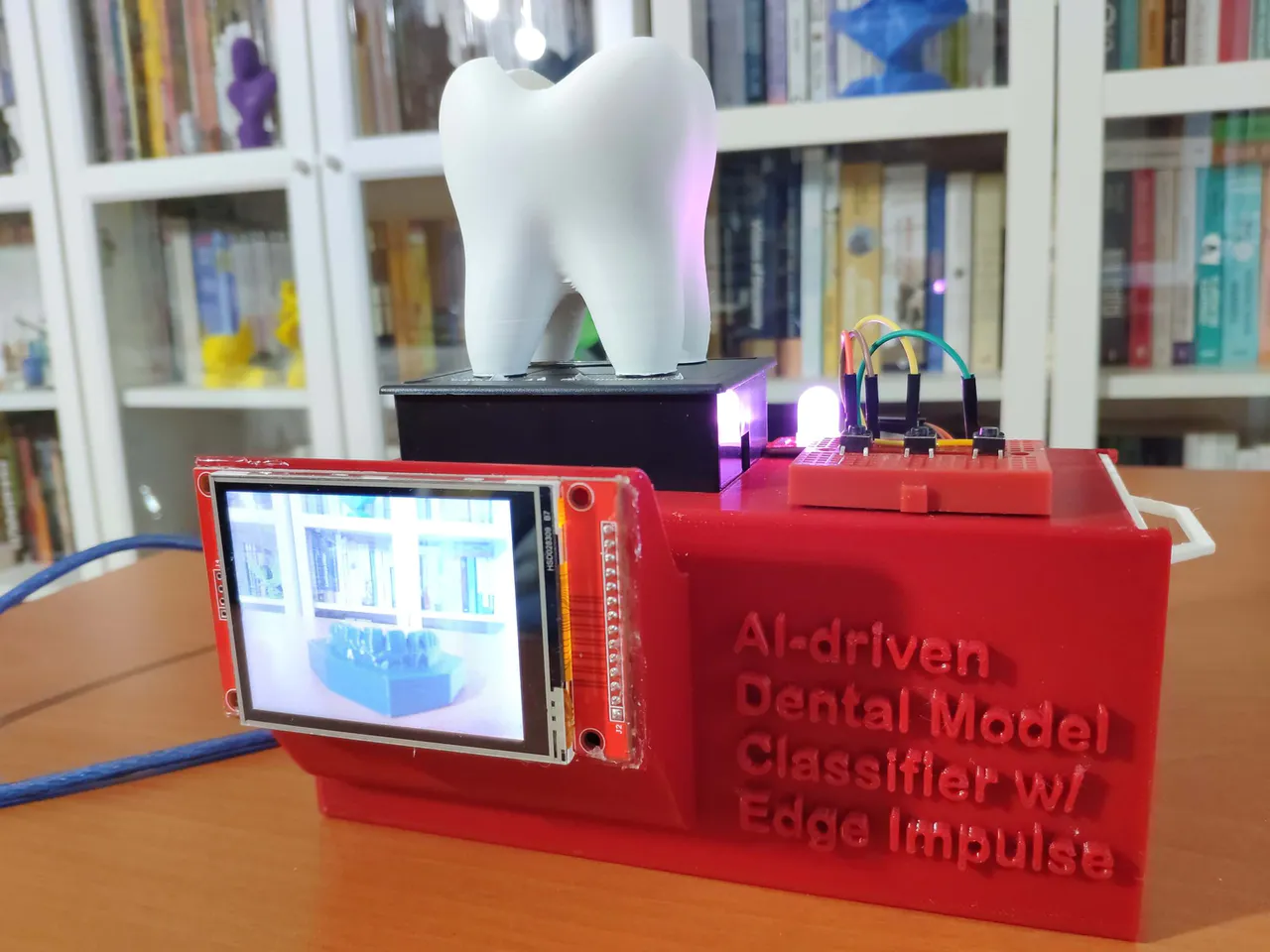
To train the Edge Impulse model, Aktar needed to track down some example dental casts. As you might expect, coming by a pile of dental casts is not the easiest thing to do, but Aktar found that it is possible to purchase STL files of dental casts. He did exactly that, then printed them with a pair of his own 3D printers: one resin, and one FDM to add variety to the cast materials. The Spresense camera was then used to capture images of the casts, which were each assigned to one of three classes — “cast," “failed,” or “implant."
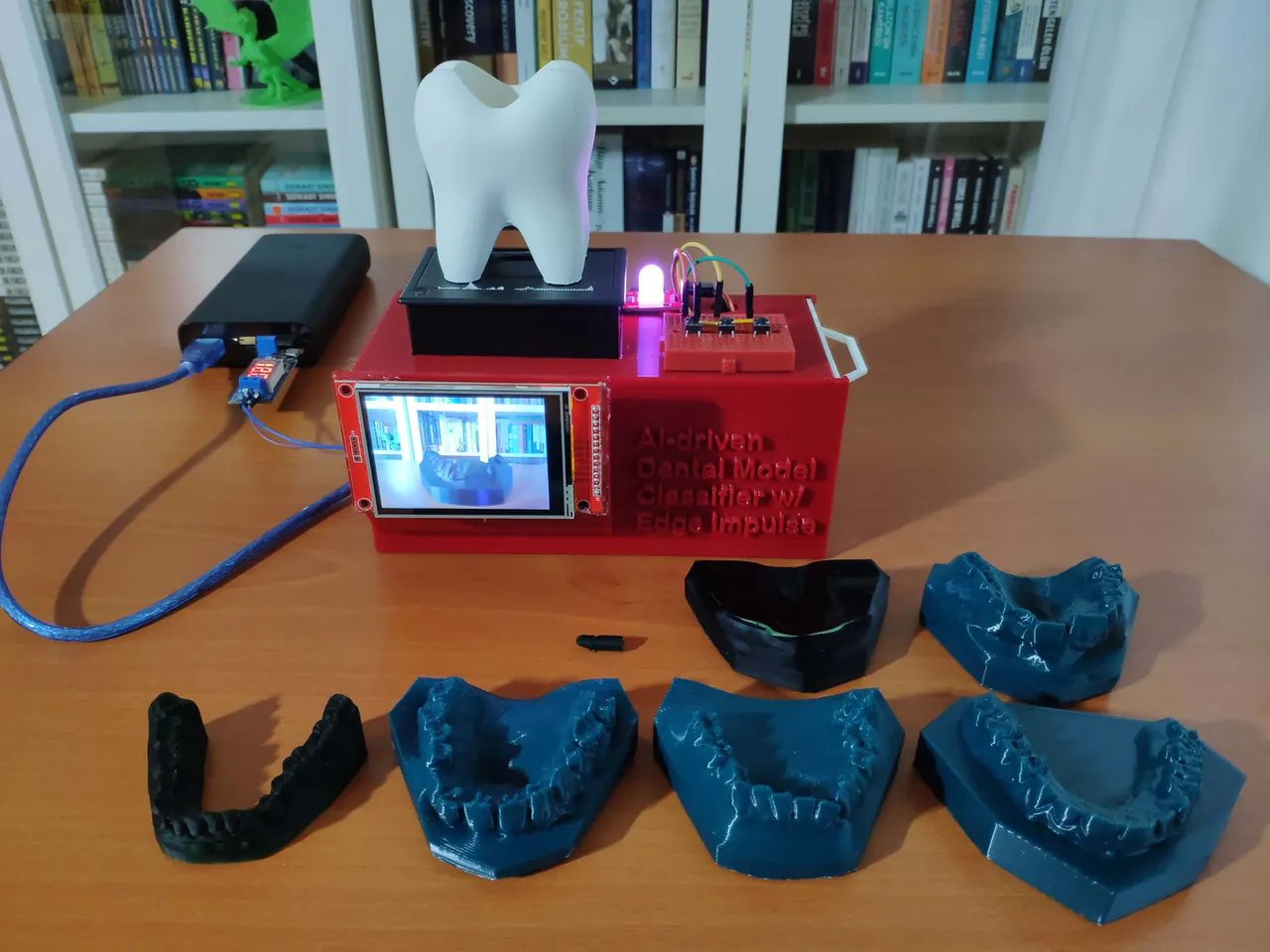
After the data collection process was all wrapped up, the images were uploaded to Edge Impulse Studio where they could be used to construct a data analysis pipeline. The labeling queue tool was used to draw bounding boxes around the casts to inform the object detection algorithm. Drawing these boxes is relatively quick, because this tool uses machine learning (who would have guessed?) to automatically draw a proposed rectangle around the objects in each image.
The prepared image data is then fed into an analysis pipeline created by Aktar that resizes them and extracts their most important features. Finally, these features serve as the inputs for Edge Impulse’s ground-breaking FOMO object detection algorithm that is 30 times faster than MobileNet SSD and runs in less than 200 KB of RAM.
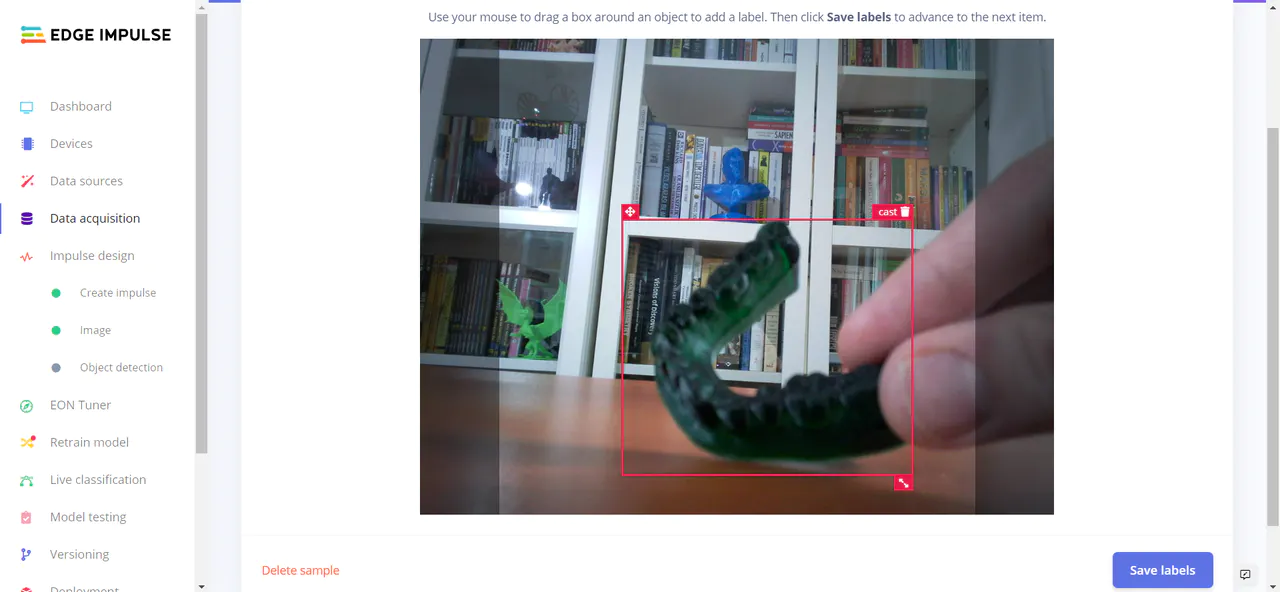
The data acquisition tool automatically sets aside some of the uploaded data to use for testing the model after training is complete. This testing step revealed that the model had achieved an average accuracy rate of 87.5%. That is a pretty impressive result for an initial prototype. And with access to more dental casts, that accuracy rate would be expected to climb even higher.
To finish the build, Aktar deployed the model from Edge Impulse as an Arduino library, then imported it into his own project with just a few clicks. With a bit of work to add support for the LCD display and the thermal printer, the software was complete and was uploaded to the Spresense development board. The completed prototype was then put through some end-to-end testing by placing dental casts inside the device and checking for the correct classification on the display screen. This testing showed everything to be working as expected, which is in line with the model testing results presented by Edge Impulse Studio.
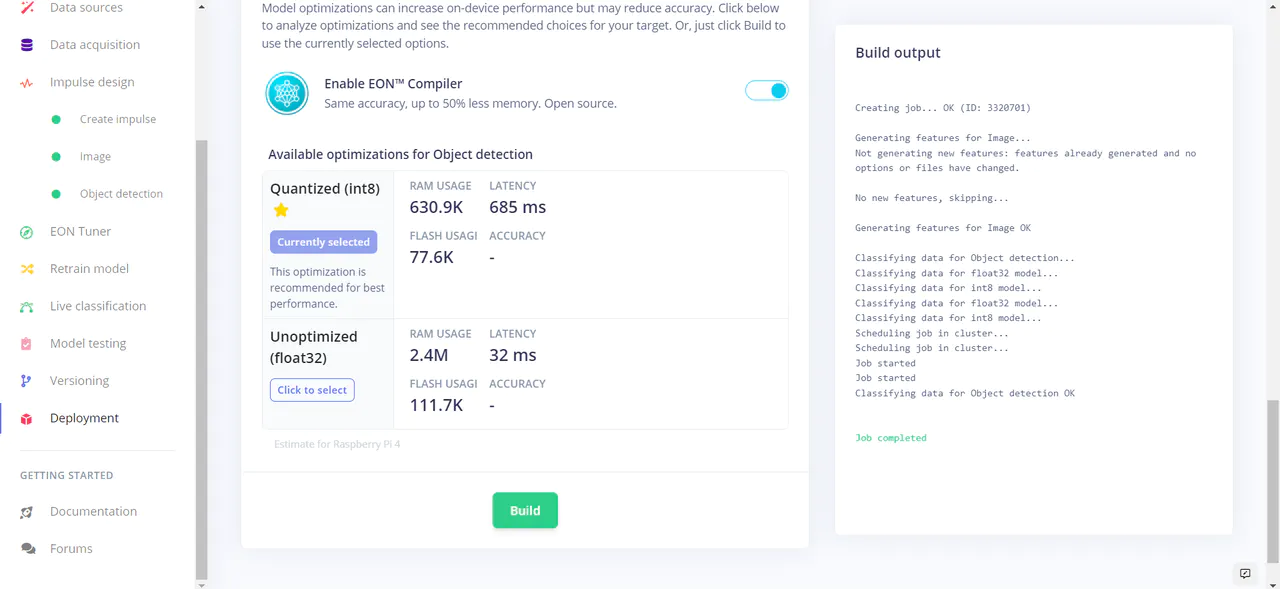
For a device that was taken from conception to completion in a short time by an individual, it is well polished. It is easy to envision a device very similar to this actually being deployed in real world dental practices. To learn how you can bring your own fantastic ideas to life, read up on Aktar’s very detailed write-up.
Want to see Edge Impulse in action? Schedule a demo today.