We may not often think about them, but pumps play a pivotal role in industrial settings, serving as the mechanical workhorses that transfer fluids, gasses, and other materials from one location to another. These essential devices are employed in a wide array of industries, including oil and gas, manufacturing, chemical processing, water treatment, and more. Pumps are used to move liquids through pipelines, circulate coolants, transport raw materials, and even pressurize gasses. The purposes they serve are indispensable to many industrial processes.
Regular maintenance is essential to ensure the uninterrupted performance of pumps. Neglecting maintenance can lead to a variety of problems, including decreased efficiency, increased energy consumption, and, in extreme cases, catastrophic pump failures. One particularly dangerous situation that can result from insufficient maintenance is bubble cavitation. This occurs when the pressure within the pump drops to a level where tiny gas bubbles form in the fluid. As the fluid pressure rises again, these bubbles collapse violently, causing shockwaves and erosion within the pump. Over time, bubble cavitation can severely damage pump components and lead to costly repairs or replacements.
Maintaining pumps in industrial settings is difficult because there are often many pumps in operation, many of which may be located in remote or inaccessible areas. Manually inspecting all of these pumps is both costly and time-consuming. As a result, businesses are increasingly turning to predictive maintenance strategies that use sensor technology and data analytics to monitor the health and performance of pumps remotely. This proactive approach helps to detect potential problems early, allowing for a timely intervention and the prevention of costly pump failures, such as those caused by bubble cavitation.
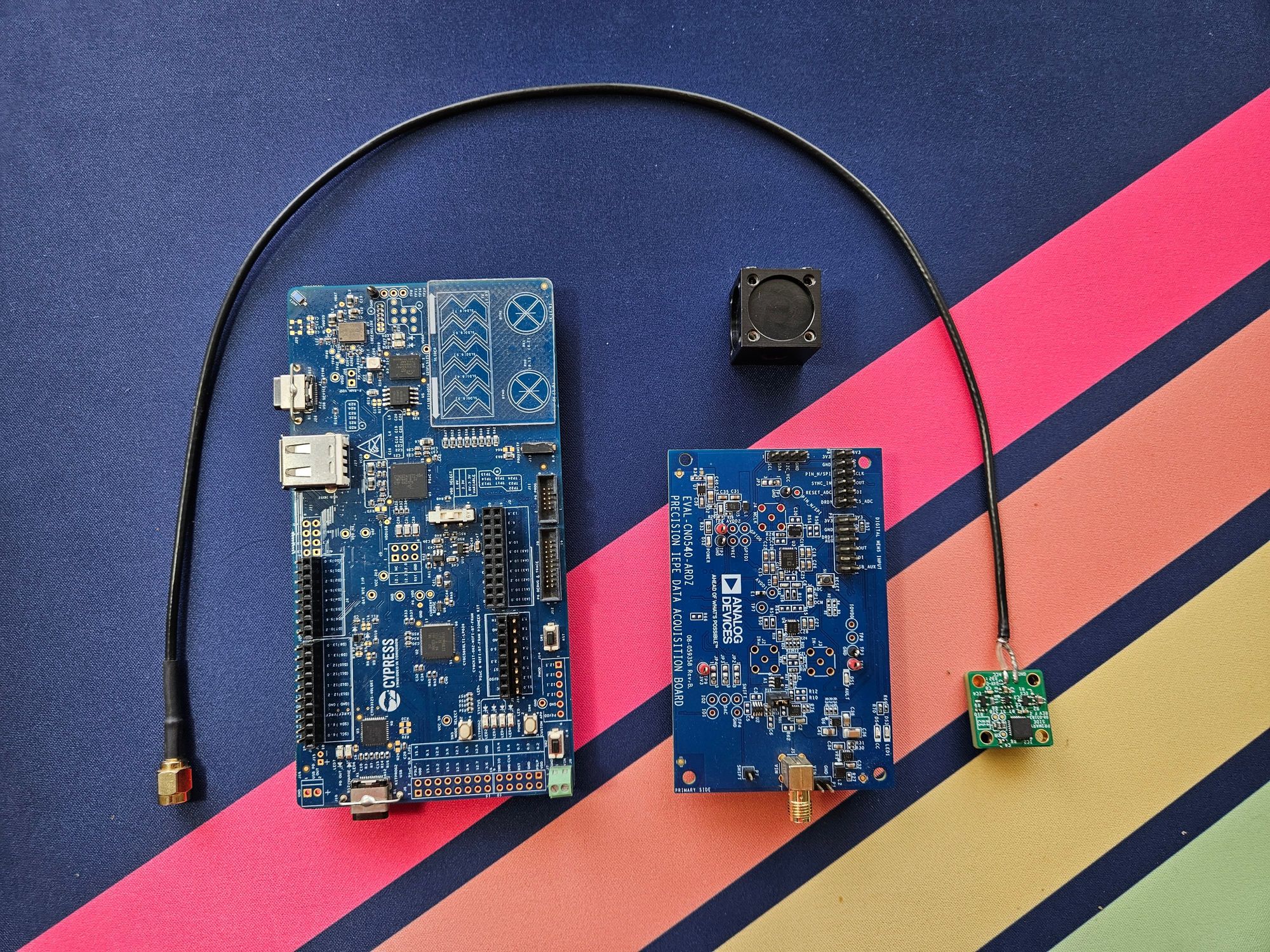
These predictive maintenance systems can take a huge load off of a maintenance crew and prevent costly equipment failures and downtime, but sometimes the systems themselves are costly and complex, which serves to hinder their widespread adoption. An engineer by the name of Pratyush Mallick believes that he has a solution to this problem, however. By leveraging a machine learning algorithm built with Edge Impulse and an inexpensive hardware platform, Mallick created a predictive maintenance system that can distinguish between the normal vibrations of a healthy pump, and the anomalous vibrations associated with issues like bubble cavitation. Through real-time detection of these issues, maintenance can be performed before failures occur.
Mallick chose to use the Infineon PSoC 6 WiFi-BT Pioneer Kit as the primary hardware platform because it is inexpensive and comes equipped with an energy-efficient, yet powerful Arm Cortex-M4 processor running at 150 MHz with 288 KB of RAM, and plenty of options for expansion to add additional sensors and other components. This was paired with an Analog Devices CN0549 Condition-Based Monitoring Development Platform, which is packed with sensors to detect vibrations. Mallick also tracked down an industrial pump to help with training and testing the model for the prototype build.
After setting up the hardware for the device, everything was in place to start the data collection process. For this step, the pump was configured to move water from one container to another, with the vibration sensor placed near the pump. Data was recorded during normal operation, and bubble cavitation was also simulated by underfilling the container that the pump drew from. Data was collected directly from the development board via a Python script, which then transferred the data to an Edge Impulse Studio project where it was automatically split into training and test datasets.
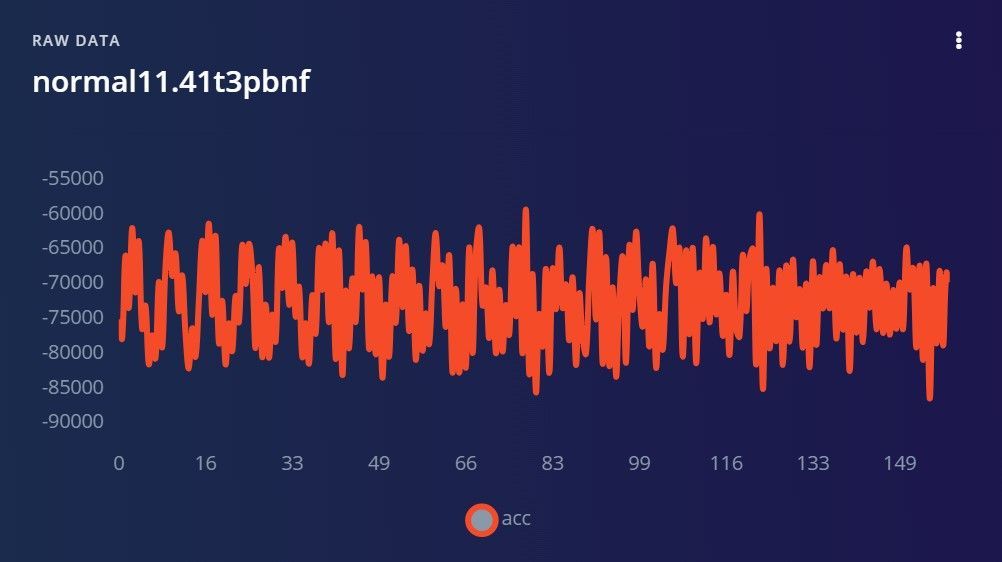
Next up, an impulse was created — the impulse defines exactly how the data is handled, all the way from the time it is captured from the sensor until the machine learning model makes a prediction. The first step in this case was a preprocessing block that split vibration measurements into 160 millisecond segments. These segments were then converted into spectrograms, which served to extract time and frequency features from the signal. This step tends to highlight the important features and patterns in measurements of vibration. The spectrograms were then forwarded into a neural network classifier that was configured to distinguish between the patterns of normal pump operation and the presence of bubble cavitation. The data augmentation tool was utilized at this stage to prevent the model from overfitting on the training data.
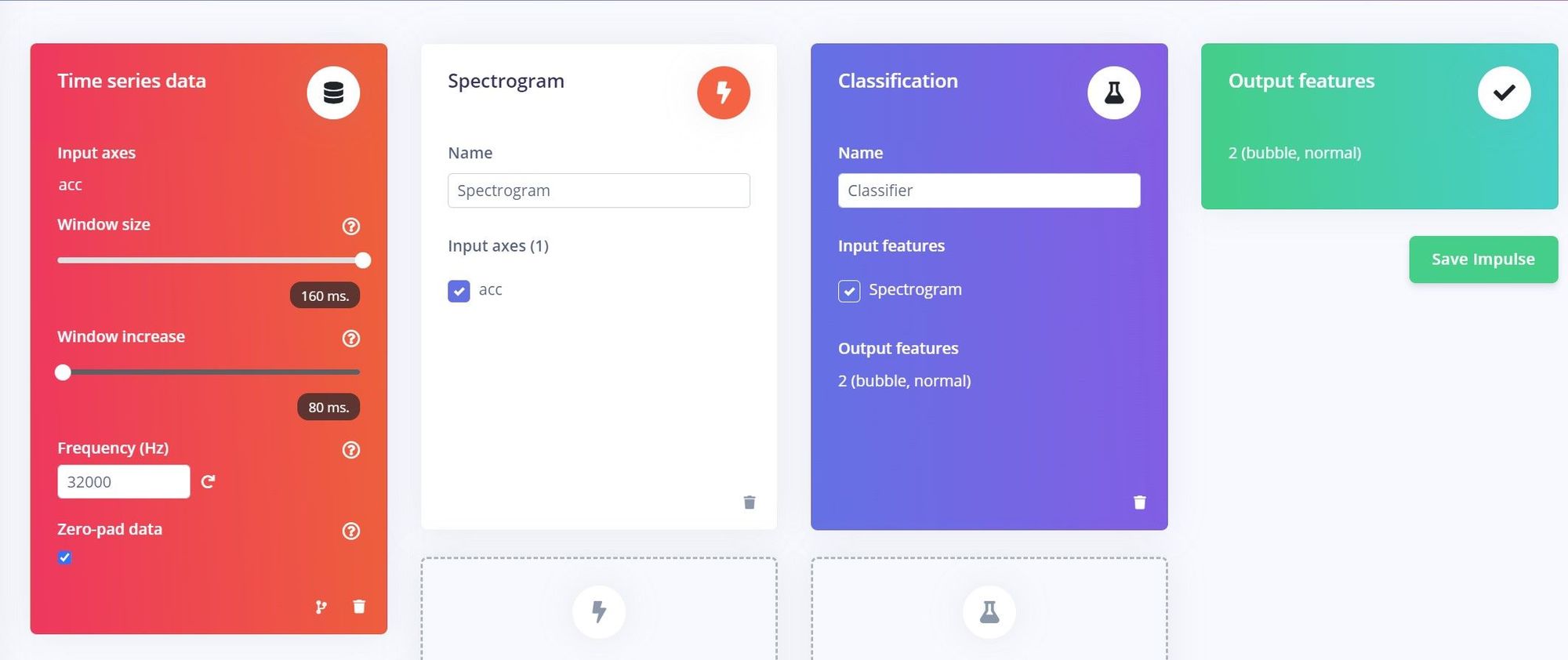
The training process was then initiated with the click of a button, and after a short time a summary of the results was presented. This revealed that, on average, the model correctly classified the sensor data 97% of the time. Clearly, that is an excellent result, but it is important to make sure that such a result is not due to overfitting. As such, Mallick ran the model testing tool, which assesses the model using a dataset that was not included in the training process. This tool showed the average accuracy rate to be better than 92%, so everything was checking out just fine.
To avoid the requirement that a network connection be available for operation, the full machine learning analysis pipeline was deployed from Edge Impulse Studio to the PSoC 6 WiFi-BT Pioneer Kit. A pre-compiled binary is available through the Deployment tool, but in this case, since Mallick was using an unsupported sensor platform, he downloaded the pipeline as a C++ library. This option gives a lot of flexibility when it comes to adding custom hardware or application logic.
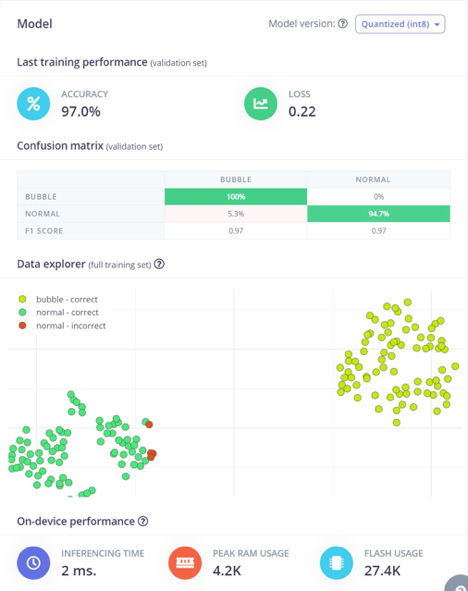
After compiling the library and flashing it to the board, Mallick found that it was operating quite well, as would be expected from the training results. While there may be some work yet to be done before this device could be put to work in a real-world setting, this prototype shows not only how inexpensive predictive maintenance can be, but also how accessible it can be. With the help of tools like Edge Impulse Studio, one can create an intelligent device without having any special expertise in the area of machine learning or embedded hardware.
Mallick lays out all of the details in his project write-up, and the Edge Impulse Studio project has also been made public if you would like to take a look. I suggest that you bookmark them for a rainy day when you have a free afternoon — that is all the time it will take to get your own prototype system up and running.
Want to see Edge Impulse in action? Schedule a demo today.