In industrial settings, few things are feared more than equipment failures. These failures frequently lead to costly downtime, production delays, and even safety hazards. To combat these challenges, many organizations have turned to predictive maintenance as a proactive solution. Predictive maintenance involves using data analytics, machine learning algorithms, and sensors to anticipate equipment failures before they occur. By continuously monitoring equipment condition and performance in this way, organizations can detect abnormalities or signs of wear and tear early on, allowing them to schedule maintenance before it is too late.
From pumps to HVAC systems, motors, conveyors, and generators, the equipment that can benefit from proactive monitoring in an industrial setting is virtually endless. Unfortunately, many decision makers are uncertain how predictive maintenance can be implemented in their organization, and the vast scope of the types of equipment to be monitored can be bewildering. The complexity and expense associated with installing all of the monitoring devices and support systems can be enough to make them drop the idea altogether. That could prove to be a huge mistake considering all of the benefits that proactive monitoring has to offer.
But does it really need to be so complicated and costly? Based on David Tischler’s latest project, the answer would seem to be a resounding “no.” In this proof of concept work, Tischler demonstrated the ease with which a predictive maintenance device can be developed for a pump by using Edge Impulse and a low-cost, commercial hardware platform. The basic principles outlined in the project could be leveraged to monitor other types of equipment as well with a few tweaks, so it is conceivable that devices of this sort could be used to monitor an entire factory’s worth of equipment.
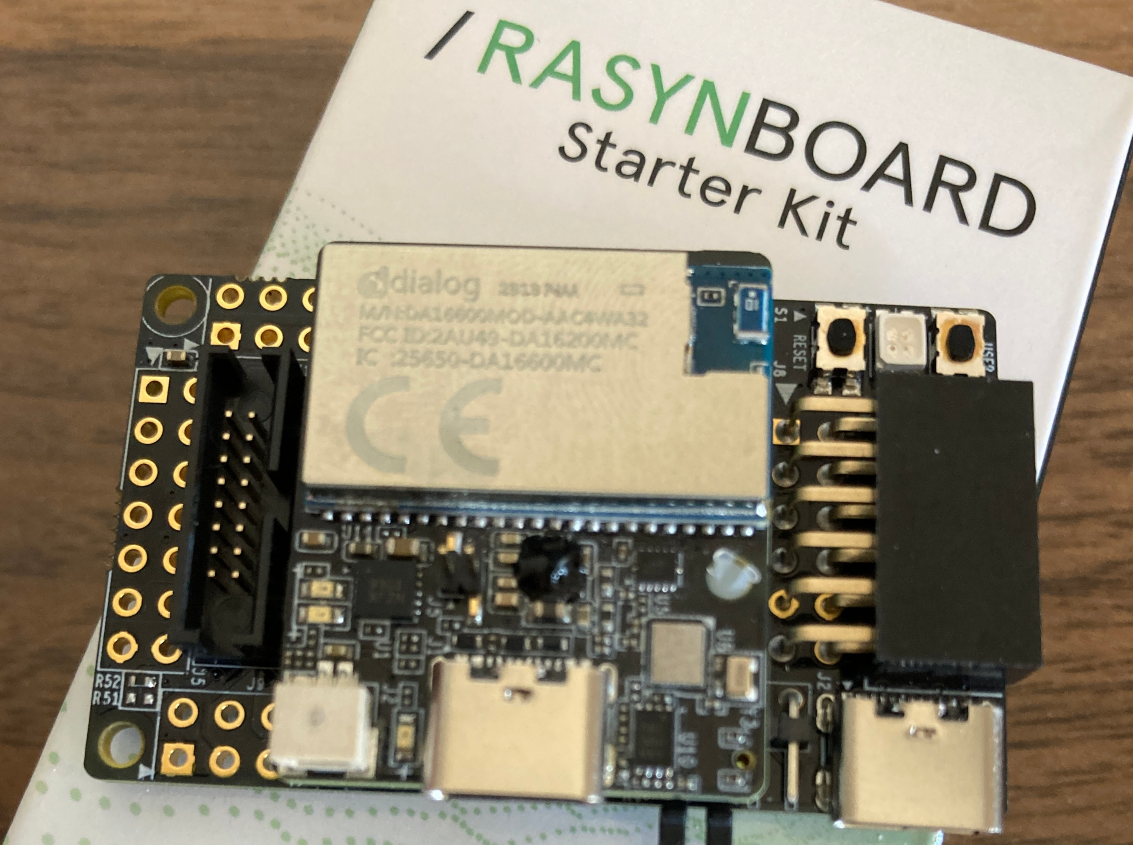
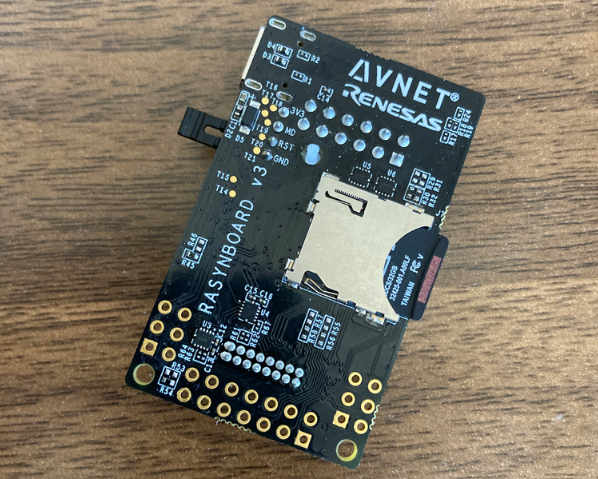
The RASynBoard development kit
Much can be learned by keeping watch over the patterns of vibration or sound emitted by a piece of equipment. When things start to go wrong, the first clues that something is about to fail are likely hidden in those patterns. In this particular case, Tischler wanted to look at a very common piece of hardware used in industry — a pump. The sound a pump makes gives information about things like the speed that it is operating at. And that, in turn, might indicate that the flow of a liquid has been restricted, or that levels of that liquid are rising to concerning levels, for example.
The basic plan involved using Edge Impulse to analyze and classify the sound that the pump makes to determine if it is running at a normal low speed, or if it has kicked into high gear and is running abnormally fast, which could indicate that trouble is brewing.
On the hardware front, Tischler chose to work with Avnet’s RASynBoard Kit. This tiny, low-cost evaluation board is practical for large-scale deployments, and it is packed with power for running advanced machine learning algorithms on-device. It comes equipped with a Renesas RA6M4 microcontroller for general-purpose computing and a Syntiant NDP120 Neural Decision Processor to accelerate machine learning inferencing. It also comes standard with sensors like an inertial measurement unit and a digital microphone, which makes it an all-in-one solution for many predictive maintenance applications.
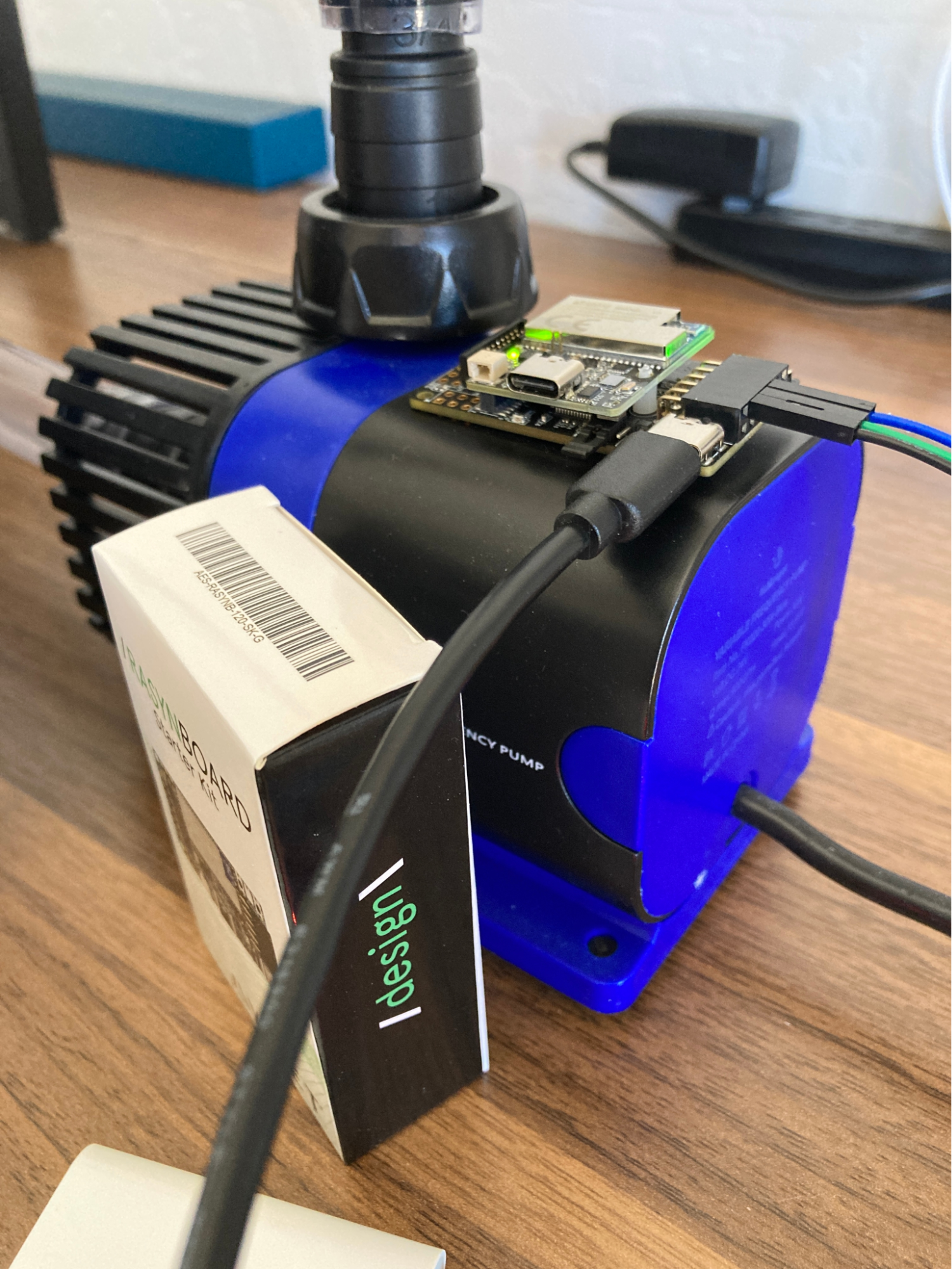
To make the integration with Edge Impulse seamless, Tischler loaded special firmware onto the RASynBoard. He walks through the steps needed to accomplish this in the project write-up. Once the setup is complete, the device can be linked to an Edge Impulse project which allows it to be used for collecting sensor data, and it also simplifies model deployment and testing.
Before a classifier can be trained, sample data must be collected for it to learn from. Tischler strapped the hardware to the pump, and collected data from it by going to the Data Acquisition page in Edge Impulse, then choosing to sample data from the microphone. He acquired one-second audio samples while the pump was running at speeds of 10 percent and 85 percent, gathering a total of 50 samples for each condition. He assigned labels to the data samples by the Data Acquisition tool, then automatically split them into train and test datasets.
With the hardware and training data all squared away, Tischler started working on the impulse design. The impulse defines how data is processed, from the time that audio is captured by the microphone until the prediction is made by the machine learning classifier. In this case, the impulse began with a step that split the audio samples into smaller segments. These segments pass into another step that extracts the most informative features from the data, before finally passing those features into a neural network classifier. The classifier will then predict if the pump is running at a low or high speed.
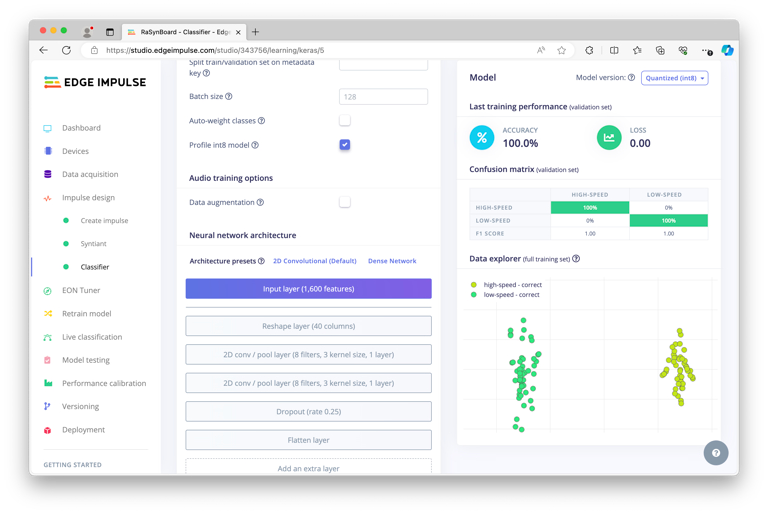
After completing the impulse design, the training process was initiated with the click of a button, presenting the results after a short time. On the first try, the accuracy of the model was found to have reached 100 percent. This is obviously excellent, but can be a sign of the model overfitting to the training data. But a look at the Data Explorer revealed a very sharp separation between the low speed and high speed data sample features, which gives confidence that the result is legitimate. The model should be capable of distinguishing between these conditions with perfect accuracy.
To get things up and running quickly, Tischler initially chose to download firmware containing the full classification pipeline. This is the fastest way to test a new model and assess its performance. But as was noted, the impulse can also be deployed as a Syntiant NDP120 library. This option allows the developer to customize the software and add their own logic, perhaps sending some type of alert if a maintenance issue is detected, for example.
After seeing the success of this proof-of-concept build, Tischler suggested using similar techniques to monitor all manner of industrial equipment. If you would like a head start on your way to monitoring your own hardware, you can clone the public Edge Impulse project to save yourself some time. Be sure to read the project write-up as well for some additional tips and tricks.