Just because the proverb “better late than never” is often repeated does not mean that it is always true. When it comes to performing preventive maintenance on industrial machinery, for example, late can be just as bad as never. A recent report by the Aberdeen Group found that, on average, the cost of unplanned downtime resulting from equipment failure is a jaw-dropping $260,000 per hour. With downtime typically lasting four hours, that means that costs exceed one million dollars per incident. Clearly, properly maintaining equipment to prevent these incidents is critically important to businesses. And this is all the more relevant in the present environment of supply chain issues that are delaying the receipt of replacement parts and further exacerbating these problems.
While performing regularly scheduled maintenance can prevent some problems from cropping up, there is an even more effective method to prevent machines from breaking down. Detecting when a machine is likely to have a future problem allows specific maintenance to take place in time to head off that problem and entirely prevent what could have been a costly outage. Predictive maintenance, as this practice is called, uses sensors and the power of machine learning to recognize when a future problem is looming to sound an early alarm. This may sound like a costly solution to implement that requires a lot of specialized knowledge, but as the engineers at Zalmotek recently demonstrated, predictive maintenance can be implemented inexpensively, and without a high level of expertise.
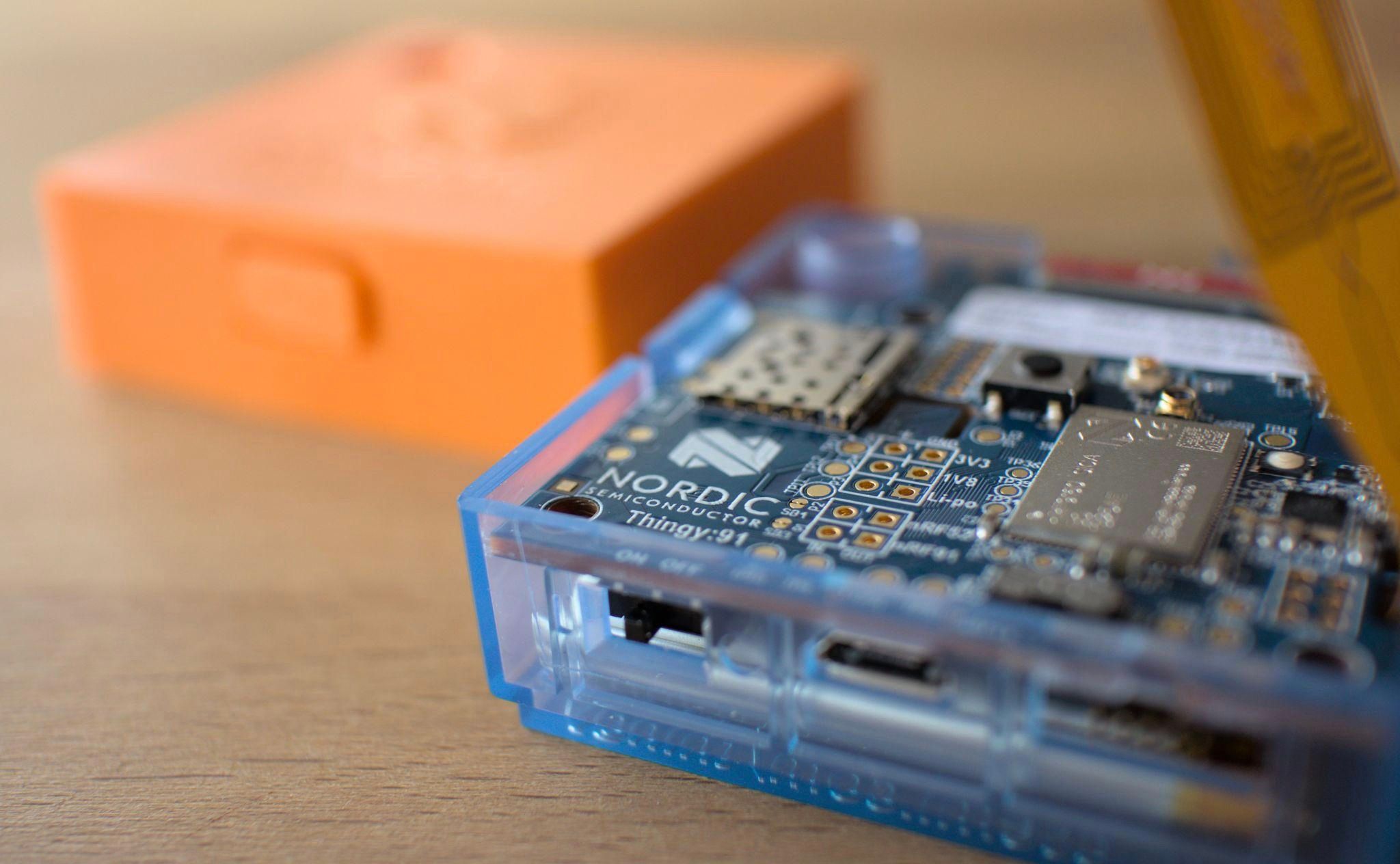
Zalomotek constructed a proof of concept device with the powerful, yet inexpensive Nordic Thingy:91 prototyping kit and the Edge Impulse platform. In their implementation, the monitor was attached to a 3D printer to look for problems before they occur, but as they note, this same method could easily be adapted to many other types of equipment, including extruders or machines with motors. Once the device has been assembled, it simply needs to be affixed to the piece of equipment to be monitored.
The Thingy:91 is an all-in-one solution, containing processing power, a host of sensors, and wireless connectivity all on the same tiny board. The 64 MHz Arm Cortex-M4 CPU, 256 KB of RAM, and 1 MB of flash memory make this kit ideal for running Edge Impulse machine learning pipelines that have been optimized for edge computing devices. The built in low-power accelerometer is perfect for detecting abnormal conditions in any type of equipment that moves or vibrates. There is also a cellular modem that enables the Thingy:91 to wirelessly communicate with other devices.
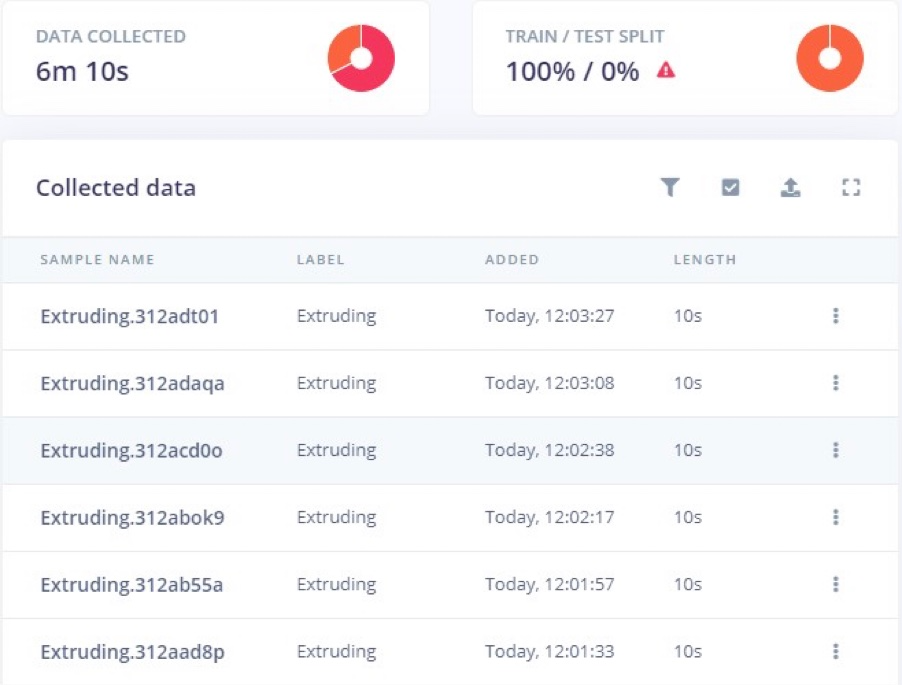
The idea behind this device is to analyze accelerometer data to determine what state the monitored machine is in, and also to look for any previously unseen but abnormal conditions, which would indicate a problem of some sort may be on the horizon. Before building the machine learning models, it was first necessary to record accelerometer data from the 3D printer in the states that Zalmotek wanted to recognize (extruding - correct, idling - correct, extruding - incorrect, idling - incorrect). After linking the Thingy:91 to Edge Impulse Studio, data was collected from each of these states, and was automatically uploaded to Edge Impulse where it could be further analyzed.
The next step in the process was to construct the data analysis impulse. This consisted of a spectral analysis that calculates the most important features present in the dataset. By doing this preprocessing of the data, downstream steps can perform with greater accuracy, and also require fewer CPU cycles. The extracted features were then fed into both a neural network classifier and a K-means anomaly detection algorithm. The neural network is capable of detecting any known states that the model has been trained to recognize, whereas the anomaly detector can recognize any abnormal activity, to make sure no machine faults are missed.
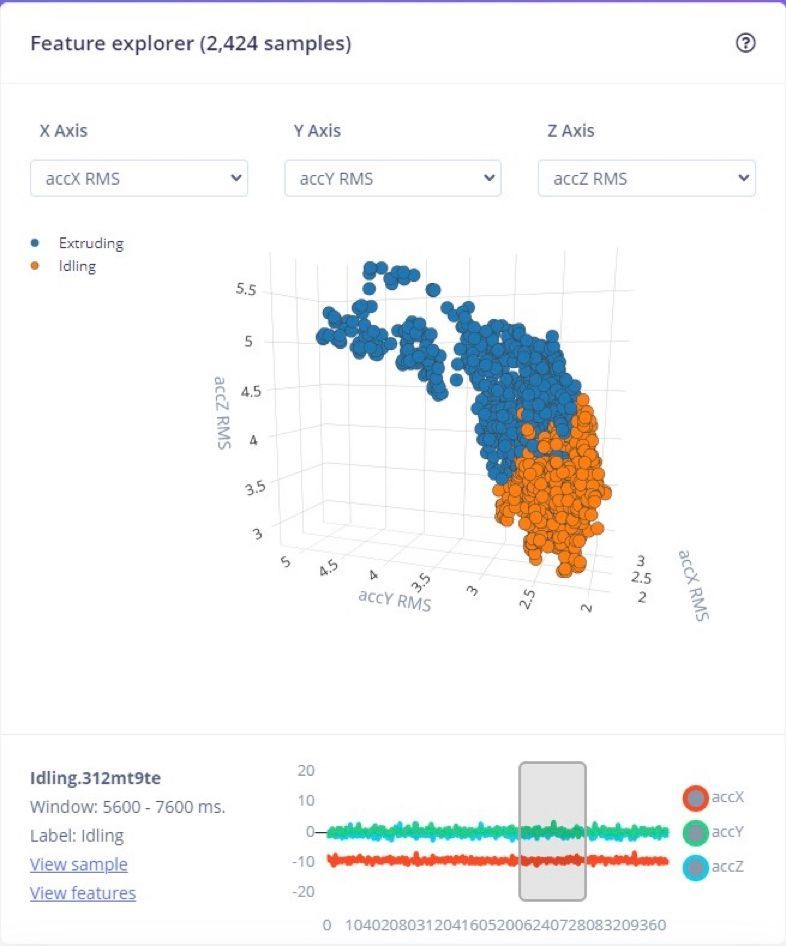
After training, it was found that the neural network classifier was capable of accurately identifying accelerometer data in 73% of cases. That is not a bad result at all considering that a very small amount of training data was collected. With a larger dataset this accuracy rate should be well over 90%. Zalmotek also examined the results of training the anomaly detector and found that it appeared to be working as expected, so they continued on to the next stage of development.
Naturally, one would want the device to be self-contained and not reliant on a connection to a cloud resource for operation, so the Edge Impulse models were deployed directly to the Thingy:91. Since this board is fully supported by Edge Impulse, a custom firmware image can be downloaded and flashed to it that contains the models. This is a super fast way to get up and running, but if further customization of the device is necessary, the analysis pipeline can also be exported as a C++ library, with no external dependencies, that is a snap to integrate into an existing codebase.
That is all there is to it. I did tell you upfront that it would be simple, right? You still do not believe me? Then take a look at the project documentation to see for yourself.
Want to see Edge Impulse in action? Schedule a demo today.