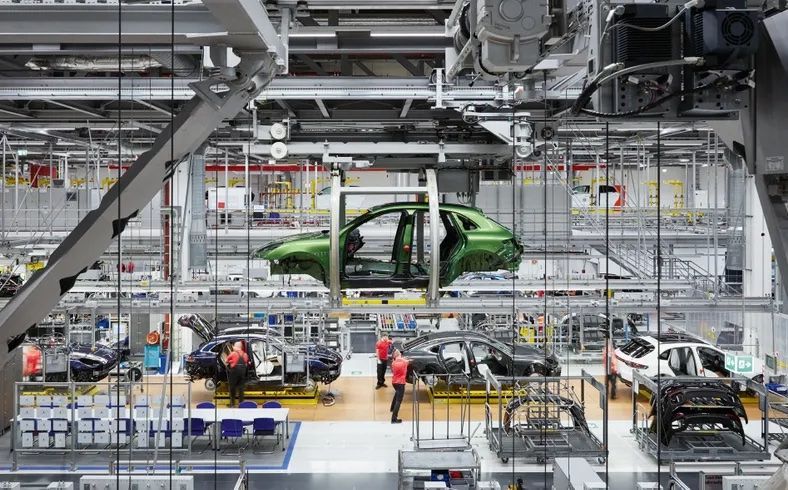
This article was originally published on Wevolver.
For over a decade there is a steady rise of the Internet of Things (IoT) paradigm, which is propelled by the proliferating number of internet-connected devices. Nowadays, the billions of connected devices offer businesses unprecedented opportunities to collect and analyze data from the physical world to improve their business processes. These devices range from microcontrollers residing in printers, cars, coffee machines and white appliances, to computationally powerful smartphones and tablet computers. Hence, they enable a host of enterprise IoT applications in many industrial sectors. In several cases, they also boost novel and successful business models, which lead enterprises to ride the wave of IoT applications.
In most cases, enterprises process IoT data within edge clusters or the cloud, rather than within edge devices and microcontrollers. The advent of Embedded Machine Learning and TinyML, inverts this paradigm, pushing the intelligence of the applications to the edge of the IoT networks. As illustrated in the first article of this series, this provides significant benefits including:
- Significant savings on bandwidth, energy, and storage resources.
- Opportunities for faster and low-latency data processing
- Facilitate real-time control applications and boosts timely decisions.
- Make use of large amounts of data from unconnected devices
These benefits are tangible and have clear business relevance. The ability of enterprises to use more data and process at the edge of the network enables new efficiencies in business, directly translating to monetary benefits and improving corporate bottom lines. Embedded machine learning is neither a new hype nor an engineering exercise for hackers and computer geeks. It is a game-changer in the Artificial Intelligence and the Internet of Things computing space, which can elevate enterprise productivity. The best witness for this is the significant number of ROI (Return-on-Investment) generating use cases currently deployed by industrial enterprises worldwide. The following paragraphs present a representative set of such use cases.
1. Intelligent Asset Management and Industrial Maintenance
Most industrial enterprises maintain their assets based on a preventive maintenance approach; the latter hinges on servicing or replacing assets such as machinery and tools in regular intervals. These intervals are dictated by their nominal End-of-Life (EoL), which is provided by the OEM (Original Equipment Manufacturer). This approach helps to avoid catastrophic production downtimes, as assets are typically maintained before they break down. Nevertheless, preventive maintenance leads to sub-optimal utilization of expensive assets, given that assets are always replaced well in advance of their EoL.
The advent of Industry 4.0 and of the Industrial Internet of Things enables industrial enterprises to implement condition-based monitoring of their assets. Leveraging digital data from sensors (e.g., vibration sensors, temperature sensors, thermal images) and asset management systems (e.g., product quality data, oil analysis), enterprises can nowadays get real-time insights on the status of industrial assets like tools and machinery [1]. Furthermore, using machine learning algorithms, they can also derive predictive insights on the Remaining Useful Life (RUL) of their assets. In several cases, credible RUL estimates enable industrial enterprises to shift preventive maintenance to predictive maintenance [2]. Predictive maintenance is the ultimate vision of Maintenance and Repair Operations, which leads to the best possible Overall Equipment Efficiency (OEE). Condition-based monitoring and predictive maintenance help enterprises improve the utilization of their assets, reduce production downtimes, eliminate waste due to equipment failures, and to schedule maintenance tasks at an optimal time. Predictive maintenance is considered as one of the killer apps of the fourth industrial revolution (Industry 4.0): It has a tangible ROI and is applicable in almost all industrial sectors, including for example manufacturing, energy, construction, smart buildings, oil and gas, and mining.
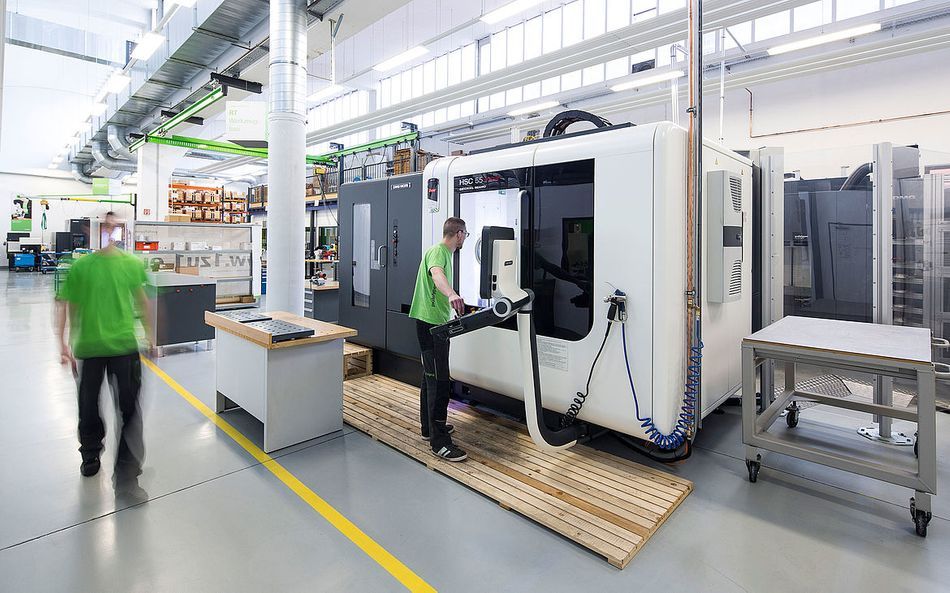
Most of the state-of-the-art predictive maintenance deployments transfer and analyze data in the cloud. This approach is bandwidth and energy-savvy while presenting limitations in its operationalization. For example, the prediction of a failure based on cloud-based machine learning analytics is not always fast enough to allow for proper remedial or preventive actions. Embedded Machine Learning adds significant value to conventional predictive maintenance and condition monitoring: It produces real-time insights and enables real-time decisions. The execution of machine learning directly on data collection devices or microcontrollers inside the machinery, enables industrial enterprises to derive timely and accurate insights about the status of the various assets. This unblocks the potential of real-time decisions based on the actual equipment condition.
Real-time industrial maintenance based on embedded machine learning is an excellent use case for OEMs as well. Specifically, OEMs can enhance their machinery with intelligent fault and anomaly detection functionalities, leveraging machine learning inside their products. They can accordingly provide such intelligence functionalities as a service to their customers to enable novel business models such as Maintenance as a Service. Overall, Embedded Machine Learning enhances the efficiency of state-of-the-art Predictive Maintenance applications in ways that increase assets’ utilization and optimize their service windows.
2. Quality Management and Zero-Defect Manufacturing
Machine learning has recently opened new horizons in quality management for manufacturing and production operations. Specifically, it empowers the concept of predictive quality [3] i.e., the ability to predict and anticipate quality issues before they occur. In this direction, machine learning techniques (including deep learning) are applied over large amounts of data from production lines. The goal of the algorithms is to proactively identify conditions or patterns that lead to defective products. Based on these patterns, plant managers can take remedial actions that prevent the defect from occurring. Furthermore, machine learning techniques can be used to optimize patterns associated with the optimization of other parameters such as cost and environmental performance.
Embedded machine learning adds significant value to the above-listed quality management use cases. Specifically, it provides the means for extracting predictive insights on potential defects based on the processing of data inside the equipment. These insights can be combined with information from cloud analytics towards identifying processes and control parameters that lead to quality problems. Likewise, they can be used to optimize multiple parameters at the same time, leading to Zero Defect Manufacturing [4]. Thus, embedded machine learning equips plant managers and quality engineers with a new wave of real-time, asset-level information about defects, which complements existing knowledge about quality management problems. As such it enables enterprises to excel in the implementation of their quality management strategies such as Total Quality Management (TQM)[5] and Six Sigma.Overall, industrial enterprises can leverage embedded machine learning to complement their existing quality management knowledge in order to improve product quality, while reducing production times and costs.
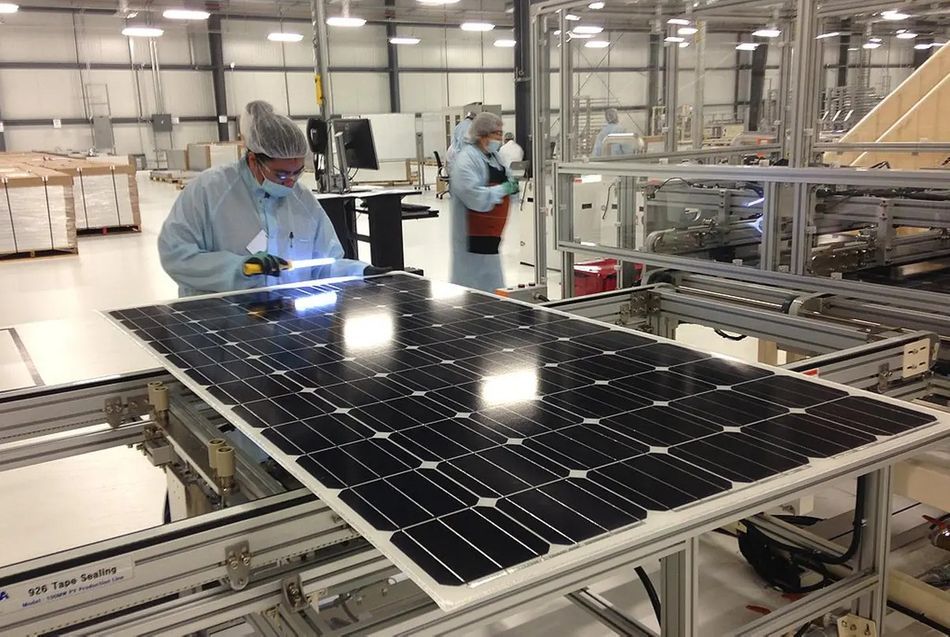
3. Occupancy Monitoring in Facilities Management
For over five years, IoT systems and applications have a transformative impact on smart buildings and facilities management applications. The deployment of sensors within buildings and other real estate assets enables property owners to access real-time, up-to-date information about the status of their properties. Based on this information they can optimize the operation of HVAC (Heating Ventilation and Air Conditioning) systems towards saving costs and improving their environmental performance. In this direction, occupancy monitoring applications are very important.
Based on the processing of data from temperature and other sensors, it is possible to extract accurate insights about the occupancy of rooms and other physical assets like desks, computers, and office spaces. This is a key for optimizing energy efficiency and maximizing comfort for tenants. Furthermore, it provides facility managers with real-time insights on the utilization of shared assets, which enables them to plan for the assets’ use and boosts their overall productivity. During the past few months, there is a surge in demand for such occupancy monitoring applications because of the COVID19 pandemic outbreak. The latter has led to the implementation of massive teleworking policies, which make it much more challenging for facility managers to monitor and anticipate assets’ occupancy patterns. Sensors and IoT applications come to their rescue, by providing credible and timely information about the actual presence of tenants in the various spaces.
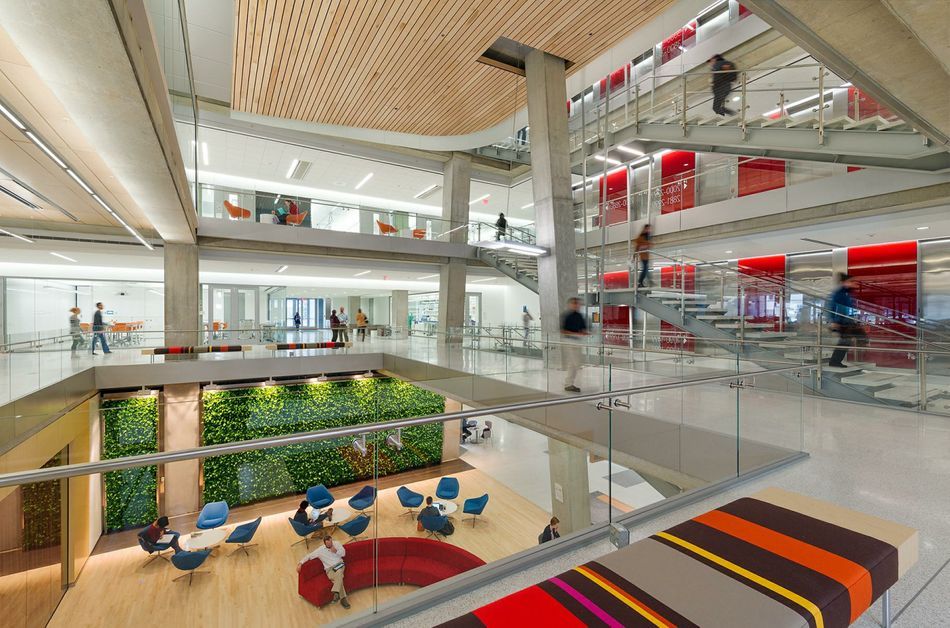
In facility management contexts, Embedded Machine Learning improves the sustainability and accuracy of occupancy management applications. Specifically, it makes it possible to run statistical data analysis within the occupancy monitoring sensors, rather than having to aggregate multiple sensor values through a cloud gateway. This increases the accuracy and the timeliness of the monitoring, while also contributing to a reduced CO2 footprint. The latter is very important, given that facilities managers are turning to IoT to reduce their emissions and catch ambitious sustainability targets. In this way, they improve their brand image and boost their compliance to emerging suitability related regulations [6]. For instance, the recent New York City Climate Mobilization Act (CMA) demands more energy efficiency from buildings. Specifically, it specifies that buildings over 25,000 square feet must reduce their greenhouse gas emissions by 40% by 2030 from a 2005 baseline, and by 80% by 2050. Overall, embedded machine learning is a powerful tool for the next generation of pervasive and energy-efficient facility management applications.
4. Cattle Monitoring
During the last couple of years, IoT deployments and embedded devices are penetrating the agri-food sector and enabling precision agriculture applications [7]. As a prominent example, sensors and pervasive devices like cameras, beacons, RFID tags and specialized embedded sensors (e.g., rumen sensors) are increasingly deployed on animals to allow farmers to monitor their livestock. To this end, relevant IoT applications tend to transfer raw data about the status of the cattle to the cloud for proper analysis. Nevertheless, this approach can be inefficient or even impossible in several scenarios, such as cases where much of the cattle reside in outdoor environments that span thousands of hectares. In such settings network connectivity (e.g., short-range IoT networks) may not suffice for supporting the Quality of Service (QoS) required in the data aggregation process. Moreover, battery-powered equipment is typically required, which creates energy autonomy issues.
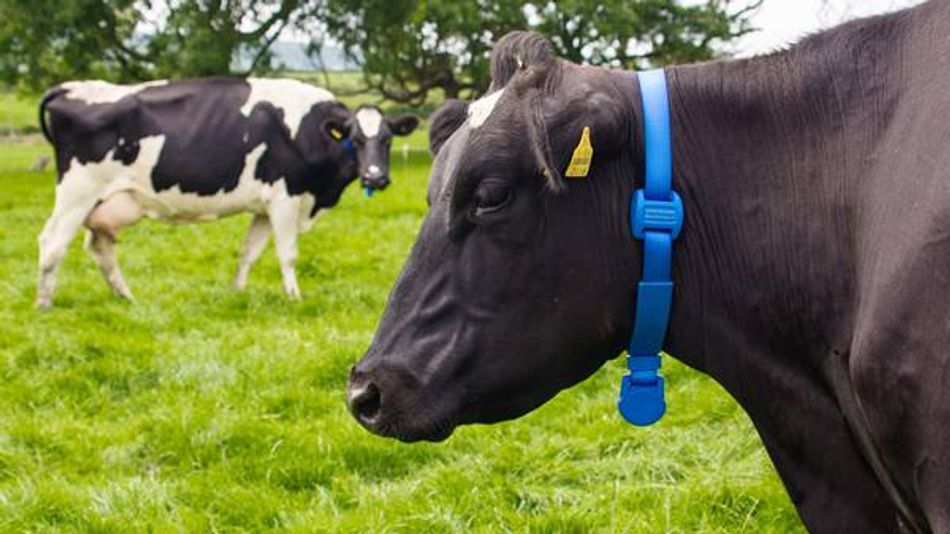
Embedded machine learning and TinyML provide substantial help in alleviating these limitations. The analysis of the data happens on the animal, which limits the amount of data that needs to be transferred to the back-end of the application. Instead of collecting data continually, the deployment of machine learning on the embedded devices enables the transfer of data at regular (e.g., hourly) intervals without any essential loss in information about the context of the animal. Farmers are provided with insights about the status of the animal and its activities (e.g., resting, fondling one another, roaring in pain or anger). Likewise, information about the heat of the animal can be provided. These pieces of information enable farmers to make educated decisions about production processes like milking and slaughtering. Overall, Embedded Machine Learning helps farmers harness the benefits of accurate cattle monitoring systems in scenarios where conventional cloud processing is not a possible or effective option.
5. Crisis Management
Machine learning and computational intelligence techniques are also used for crisis management and civil protection applications, including example earthquakes and wildfire prediction [8]. In this direction, data from various sensors are usually aggregated and processed in the cloud. However, in crisis management, time is the most important resource: The success of crisis management operations depends heavily on the timeliness of the predictions of crisis management indicators. For example, the earlier identification of earthquake warning signals can lead to faster and more effective actions. This is an area where embedded machine learning provides significant value over the state-of-the-art solutions for earthquake indicator predictions.
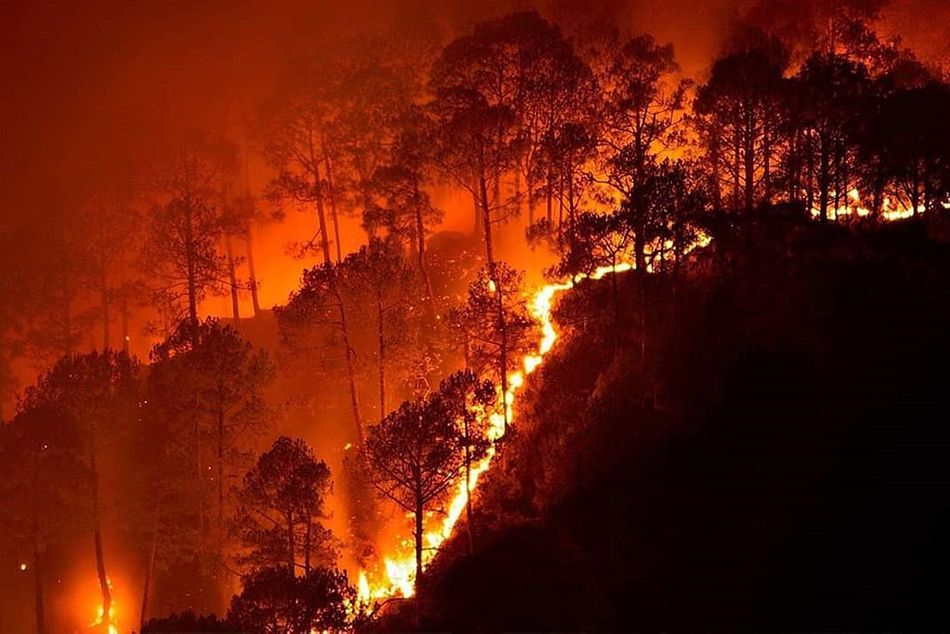
When it comes to wildfires management, embedded machine learning can deliver reliability and deployment benefits, similar to the case of cattle monitoring. In particular, the execution of statistical models inside embedded sensors can facilitate the timely prediction of wildfires without a need for robust network connectivity and battery-powered devices. This is another area where embedded machine learning adds value over mainstream cloud-based deployments.
Conclusion
Previous paragraphs presented five industrial applications of embedded machine learning. The given list is not exhaustive but rather indicative of how embedded machine learning adds tangible business value to various industrial applications. Embedded machine learning is a perfect match for a wide range of other applications. For example, in precision agriculture, it can be used to detect plant diseases directly on the plant, rather than requiring aggregation and analysis of various data streams in the cloud. As another example, it can enable accurate cold storage intelligence applications that analyze temperatures directly on sensitive products (e.g., food, beverage, and pharma products) rather than having to estimate temperature abnormalities using the ambient temperature. By and large, embedded machine learning unlocks a virtually unlimited number of innovation opportunities in many different sectors.
The development and deployment of embedded machine learning applications in industrial settings is not however an easy way out. Every implementation step must be well planned towards meeting stringent industrial requirements. From the selection of the proper embedded device to the acquisition of adequate training data and the implementation of the proper machine learning model, developers and deployment must make careful and well-educated choices. The spectrum of implementation challenges spans both the embedded computing and the machine learning space. Hence, there is a need for combining knowledge and tools from both worlds.
Edge Impulse alleviates many of these challenges through centralizing access to knowledge, resources, and tools needed for embedded machine learning development. Using Edge Impulse tools, developers can produce proof-of-concept applications just in a few minutes. At the same time, enterprises can find a wealth of resources that will help them meet demanding requirements. This is the main reason why many enterprises from different sectors trust Edge Impulse for their embedded machine learning developments.
The next article of the series sheds light on the practical implementation of embedded machine learning and the challenges that it entails. Understanding these challenges is key for appreciating the value of joining the vibrant Edge Impulse community.
References
1. W. Zhang, D. Yang and H. Wang, "Data-Driven Methods for Predictive Maintenance of Industrial Equipment: A Survey," in IEEE Systems Journal, vol. 13, no. 3, pp. 2213-2227, Sept. 2019, doi: 10.1109/JSYST.2019.2905565.
2. M. Compare, P. Baraldi and E. Zio, "Challenges to IoT-Enabled Predictive Maintenance for Industry 4.0," in IEEE Internet of Things Journal, vol. 7, no. 5, pp. 4585-4597, May 2020, doi: 10.1109/JIOT.2019.2957029.
3. Bai, Yun & Sun, Zhenzhong & Deng, Jun & Li, Lin & Long, Jianyu & Li, Chuan. (2017). Manufacturing Quality Prediction Using Intelligent Learning Approaches: A Comparative Study. Sustainability. 10. 85. 10.3390/su10010085.
4. Eleftheriadis, R., Myklebust, O.: A Quality Pathway to Digitalization in Manufacturing thru Zero Defect Manufacturing Practices. International Workshop on Advanced Manufacturing and Automation, pp. 187-191 (2016)
5. Talib, F., and Rahman, Z. (2012), “Total quality management practices in manufacturing and service industries: A comparative study”, International Journal of Advanced Operations Management, Vol.4, No.3, pp. 155-176.
6. A. -E. M. Taha and A. Elabd, "IoT for Certified Sustainability in Smart Buildings," in IEEE Network, doi: 10.1109/MNET.011.2000521.
7. D. Shadrin, A. Menshchikov, A. Somov, G. Bornemann, J. Hauslage and M. Fedorov, "Enabling Precision Agriculture Through Embedded Sensing With Artificial Intelligence," in IEEE Transactions on Instrumentation and Measurement, vol. 69, no. 7, pp. 4103-4113, July 2020, doi: 10.1109/TIM.2019.2947125.
8. O. Elsarrar, M. Darrah and R. Devine, "Analysis of Forest Fire Data Using Neural Network Rule Extraction with Human Understandable Rules," 2019 18th IEEE International Conference On Machine Learning And Applications (ICMLA), Boca Raton, FL, USA, 2019, pp. 1917-19176, doi: 10.1109/ICMLA.2019.00308.